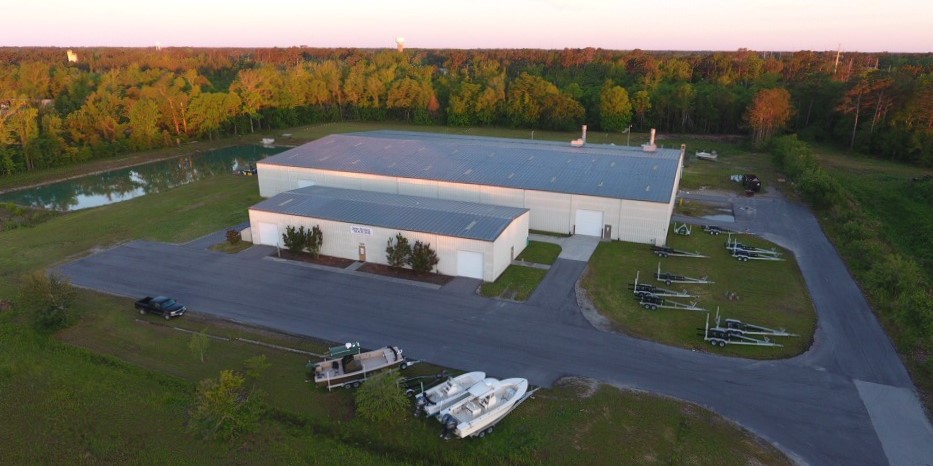
The Jones Brother factory was specifically designed to build boats. The structure was completed in 2001 and was fully operational in mid-2002. The two main buildings total 50,000 sq. ft. with plenty of room for future expansion.
Climate Controlled Environment – Buried in the cement floor is a five-mile network of water pipes used to heat the building and maintain the resins, gel coats and molds at a constant temperature. We are able to heat over an acre of enclosed manufacturing facility with only 400,000 BTUs – less than the average home. This climate control system simplifies the manufacturing process by maintaining a very controlled environment for the materials used in boat construction, and allows us to consistently deliver the best boat possible. Most boat manufacturers have a difficult time making seasonal adjustments with lamination schedules caused by large temperature variations. Our plant maintains “laboratory” conditions every day.
Powered by Air – A great deal of effort went into designing the air system that supplies most of the tools at the factory. Wherever possible, air tools are used during manufacturing. They last far longer, are much safer and more efficient than electric tools. We use “rotary screw” compressors which are extremely efficient and durable. They’ve been running almost non-stop since the plant opened.
A lot of thought also went into our electrical power systems. For efficiency, like most factories, the electrical equipment runs on three phase power. However, due to the reliance on the air systems and efficient use of our power systems, we are able to run the entire factory on less than 480 amps service. When the local power company ran an assessment of the plant, they found it was the most efficient operation they had ever seen.
Eco-Friendly – The manufacturing plant is extremely ecologically and environmentally friendly. The air filtration system works so well that employees are not required to wear respirators during lamination. The resins and gel coats used in construction produce the lowest emissions possible with current technology. Even the flotation foam produces zero harmful emissions. These materials and compounds are expensive, but they do the least harm to the environment and help provide a safe workplace for our employees.
Our company also believes in eliminating as much waste as possible during construction – we don’t like adding to landfills or generating unnecessary waste. The molds were designed to reduce the trimming and keep waste to an absolute minimum, which reduces the manufacturing costs for our company.
The creeks and salt marshes behind the manufacturing plant produce some of the best shellfish and shrimp in the area, and most of the employees at the plant are connoisseurs of good seafood (Southern style). There is a great deal of self-interest in keeping the local environment healthy and bountiful.
Molds – Success for a boat company is heavily dependent on the quality of the molds used in construction, and the care and precision that went into their creation. At Jones Brothers, all of the fiberglass molds were conceptualized, designed and hand built in our factory. We spent a great deal of time and effort to create perfect molds, which can consistently produce quality parts time after time. Great molds, and the talented people that use them, help create the boats that live up to our high expectations.
Woodshop – The name “Woodshop” is a holdover from the good old days – no wood is used on any of the boats currently manufactured by Jones Brothers. Nowadays, the woodshop cuts the foam and other composite pieces that will be used by Lamination and Small Parts.
Lamination – Lamination builds the hull, stringers, and floor. These major components of the boat are assembled in Lamination, and then the hull is passed to Finishing for final assembly.
Small Parts – The Small Parts group builds the console, deck cap, hatches, and any necessary livewell, jump seats, and/or leaning posts for a boat. Most of the fiberglass parts used by Jones Brothers are built in-house to insure the quality and consistency of the finished product.
Finishing – Early in the manufacturing process, the Finishing department examines the sale order for the engine(s) and options selected by the customer. Inventory is set aside for the boat for final assembly.
When Finishing gets the hull from Lamination, and the remaining components from Small Parts, each piece gets a thorough inspection and any imperfections are fixed. Once all the parts have the proper fit and finish, the boat continues down the assembly line and finally comes together.